How Mobile Concrete Batching Plant Technology Is Reshaping On-Site Mixing
The construction industry is undergoing a technological transformation, and one of the most significant advancements driving this change is the evolution of the mobile concrete batching plant. Once seen as a secondary option to traditional stationary batching plants, mobile units have grown into powerful, efficient systems capable of delivering high-quality concrete on-demand—directly at the job site.
As global construction demands rise, especially in infrastructure, urban expansion, and remote developments, mobile batching plants are becoming the preferred choice for many contractors. This article explores how mobile concrete batching plant technology is revolutionizing on-site mixing, and how it compares to traditional ready mix concrete plant setups and stationary batching plants. We’ll also look at the current trends in the market for a concrete batching plant for sale.
The Shift Toward On-Site Mixing Solutions
Historically, the construction industry relied heavily on ready mix concrete plants. These centralized facilities produce concrete in large quantities and transport it to job sites in mixer trucks. While effective for projects near urban areas, this model often falls short in remote or time-sensitive scenarios due to:
Long transportation times that can compromise concrete quality
Higher fuel and labor costs
Limited flexibility in delivery schedules
Enter the mobile concrete batching plant—a compact, trailer-mounted or skid-mounted system that brings concrete production directly to the construction site. This not only solves logistical problems but also gives contractors greater control over mix quality and timing.
Key Technological Advancements
Recent developments in mobile plant technology have drastically improved their efficiency, automation, and performance. These upgrades are making mobile plants an attractive alternative to traditional solutions.
1. Automated Control Systems
Modern mobile batching plants now feature advanced PLC-based control systems. These allow for precise weighing, mixing, and real-time monitoring of ingredients—ensuring batch consistency and reducing human error. Automatic calibration and diagnostics further enhance reliability and reduce downtime.
2. Compact and Modular Design
Today’s mobile plants are designed to be compact without compromising capacity. Modular designs allow for quick setup and dismantling, usually within 1–3 days, compared to the weeks it can take for a stationary setup. This portability is crucial for contractors working across multiple locations.
3. Energy and Water Efficiency
Leading manufacturers have integrated water recycling systems and energy-efficient motors into mobile batching plants. These features reduce environmental impact and operational costs, aligning with global sustainability goals in construction.
4. Real-Time Data and IoT Integration
Some of the latest models include smart sensors and cloud connectivity, enabling managers to monitor plant performance remotely. Features like GPS tracking, productivity analytics, and maintenance alerts empower teams to optimize plant usage and prevent costly delays.
Advantages Over Stationary Batching Plants
While stationary batching plants remain essential for large-scale or long-term projects, mobile batching plants offer unique advantages:
Mobility: Easily transported between job sites
Quick Setup: Requires less foundation and fewer civil works
Flexibility: Ideal for short-term or fast-paced projects
Cost-Efficiency: Lower capital investment and reduced transportation expenses
Mobile plants are also a go-to solution for emergency or temporary works, such as disaster recovery, military applications, and seasonal infrastructure upgrades.
Ready Mix vs On-Site Mixing
A ready mix concrete plant is still suitable for urban or suburban areas where delivery distances are short. However, for remote areas or projects requiring frequent design changes, mobile plants deliver concrete with greater flexibility and responsiveness.
With a mobile plant, teams can:
Adjust mix ratios on the fly
Reduce wastage due to over-ordering
Maintain consistent supply during extended work hours
This level of control and responsiveness is nearly impossible with off-site ready mix concrete plant, where delays and quality degradation are more common.
The Market Outlook: Concrete Batching Plant for Sale
As demand for faster and more efficient construction rises, so does the market for mobile solutions. The concrete batching plant for sale market is experiencing steady growth, with mobile plants leading the charge. Contractors are now seeking equipment that is not only affordable but also adaptable and technologically advanced.
Top manufacturers like Aimix, ELKON, and Liebherr are introducing mobile plants with capacities ranging from 25 m³/h to 100 m³/h. These plants are well-suited for small- to medium-scale projects, including road construction, bridge works, and commercial building development.
Key buying considerations include:
Output capacity
Type of mixer (twin-shaft, planetary, pan)
Mobility (trailer or skid-mounted)
Automation level
Service and spare parts availability
Final Thoughts
The rise of mobile concrete batching plants represents a fundamental shift in how concrete is produced and delivered in modern construction. By combining portability, automation, and high-quality output, these systems empower contractors to operate more efficiently, especially in challenging environments.
As the technology continues to evolve, mobile batching plants will likely become the industry norm for many types of construction projects. Whether you’re in the market for a concrete batching plant for sale or looking to upgrade from a traditional ready mix concrete plant, mobile systems offer a future-ready solution with clear performance advantages over conventional stationary batching plants.
How IoT Sensors Cut Downtime in Industrial Mixer Operations
In today’s fast-paced industrial landscape, efficiency is crucial. Industries rely heavily on machinery, such as mixers, to maintain productivity. Any downtime can lead to significant financial losses. This is where IoT (Internet of Things) sensors come into play. They offer real-time monitoring and predictive maintenance, significantly reducing downtime in industrial mixer operations.
The Role of IoT Sensors in Reducing Downtime
IoT sensors have revolutionized industrial operations. They provide real-time data, helping operators monitor equipment health. These sensors detect anomalies before they cause breakdowns. Thus, they prevent unexpected downtime and allow for scheduled maintenance. Predictive maintenance keeps machines running smoothly and efficiently.
How IoT Sensors Work
IoT sensors collect data from various parts of the mixer. They monitor temperature, vibration, and other critical parameters. This data is sent to a central system for analysis. Operators receive alerts if any parameter deviates from the norm. This proactive approach prevents minor issues from becoming major problems.
Benefits of IoT in Industrial Mixers
IoT sensors offer numerous benefits. They ensure consistent mixer performance by reducing downtime. This leads to increased productivity and reduced operational costs. Businesses can save money on repairs and maximize output. Additionally, IoT data helps improve future equipment design and efficiency.
Case Study: Self-Loading Concrete Mixers
Consider the self loading concrete mixer for sale. These mixers benefit greatly from IoT integration. IoT sensors provide real-time data on mixer performance. This ensures that concrete quality remains high. Operators can identify potential issues before they affect the final product. As a result, companies experience fewer delays and better project outcomes.
Concrete Mixers in Different Markets
IoT technology is transforming concrete mixer operations worldwide. In Indonesia, concrete mixers are vital for construction projects. The integration of IoT sensors enhances the reliability of the concrete mixer Indonesia. Companies can complete projects on time and within budget. IoT sensors provide a competitive edge in Indonesia’s growing construction sector.
Concrete Mixer Prices in Kenya
In Kenya, the construction industry is booming. The concrete mixer price in Kenya varies based on features. IoT-enabled mixers may have a higher upfront cost. However, they offer long-term savings through reduced downtime. Businesses can justify this investment with increased efficiency and lower maintenance expenses.
Concrete Mixer Prices in South Africa
Similarly, in South Africa, IoT sensors are gaining popularity. Concrete mixer price South Africa reflects this trend. While initial costs may be higher, IoT integration offers substantial benefits. Reduced downtime, improved efficiency, and better project management make these mixers a wise investment. Companies can achieve higher profitability with IoT-enabled equipment.
The Future of IoT in Industrial Mixers
The future of IoT in industrial mixers looks promising. As technology advances, IoT sensors will become even more sophisticated. They will provide more precise data and insights. This will lead to further reductions in downtime and operational costs. Businesses that adopt IoT early will have a competitive advantage.
Conclusion
IoT sensors are transforming industrial mixer operations. They reduce downtime, improve efficiency, and lower costs. From self-loading concrete mixers to various markets like Indonesia, Kenya, and South Africa, IoT is making a difference. As industries continue to evolve, IoT will play an even bigger role. Embracing this technology is crucial for staying ahead in the competitive industrial landscape.
How to Calculate the Optimal Capacity for Your Single Girder Overhead Crane
Selecting the optimal lifting capacity for your single girder overhead crane is critical to ensuring efficiency, safety, and cost-effectiveness in your operations. The capacity of an overhead crane directly influences how much weight it can lift and move safely. Choosing a crane with the correct capacity not only helps to optimize performance but also helps to avoid unnecessary wear and tear, prevent accidents, and improve overall operational productivity.
In this article, we’ll break down the process of calculating the optimal capacity for a single girder overhead crane. We will explore the factors you need to consider, how to determine your specific requirements, and the methods involved in making an informed decision.
1. Understanding Single Girder Overhead Cranes
Before diving into the calculation, it’s important to first understand what a single girder overhead crane is and its typical use. A single girder overhead crane is a type of bridge crane where a single horizontal beam (the girder) is supported by two end trucks that travel along rails mounted on the ceiling. These cranes are typically used for light to medium-duty lifting tasks, making them ideal for environments such as warehouses, factories, and construction sites.
Single girder cranes come with a variety of lifting capacities, ranging from a few tons to several dozen tons. The crane’s lifting capacity refers to the maximum weight it can safely lift and move.
2. Identifying Your Requirements
To determine the optimal capacity for your single girder overhead crane, the first step is to identify your lifting requirements. This process involves considering the following key factors:
a. Type of Materials to Be Lifted
The type of materials you intend to lift is a fundamental consideration when determining crane capacity. Different materials have different densities and weights. For instance, lifting steel beams, concrete blocks, or machinery components will require more lifting capacity compared to lifting lighter materials like textiles or packaged goods.
Consider the heaviest material you will need to lift regularly and ensure that your crane can handle it. This will likely be the maximum load requirement for your crane.
b. Weight of Loads
Once you know the types of materials you will be lifting, the next step is to calculate the average and maximum weight of the loads. The maximum weight will often be the deciding factor in determining the crane’s capacity.
For example, if you are lifting metal parts that weigh 5 tons on average but occasionally need to lift a load weighing up to 10 tons, you should base your crane capacity on the maximum load of 10 tons, that is, select a 10 ton overhead crane.
c. Frequency of Lifting
The frequency at which you need to lift and move loads will also affect the crane capacity. If your crane will be used for high-frequency tasks, selecting a crane with an adequate lifting capacity that aligns with your needs will ensure smooth operations.
In addition, consider the types of lifts the crane will perform. Will it be used for continuous lifting? Or will it handle intermittent loads with downtime between lifts? Higher frequency operations might require a crane with a higher duty cycle, which is closely related to lifting capacity.
3. Calculating the Load Capacity
After identifying your lifting requirements, the next step is to calculate the optimal load capacity for the single girder overhead crane. Here are some steps involved in making this calculation:
a. Calculate the Maximum Weight of the Load
To calculate the maximum lifting capacity of the single girder eot crane, you must first determine the weight of the heaviest load the crane will need to lift. This can be done by multiplying the volume of the material by its density.
For example:
-
Material: Steel
-
Volume: 10 cubic meters
-
Density of steel: 7850 kg/m³
Weight of the load = Volume × Density = 10 × 7850 = 78,500 kg (or 78.5 tons)
Therefore, the crane should be able to handle at least 78.5 tons if lifting this material. However, this figure is only a guide, as overhead cranes are usually rated in increments of 1 or 5 tons.
b. Consider Additional Factors
In addition to the weight of the load itself, other factors must be taken into account, such as:
-
The weight of lifting accessories: Slings, hooks, and hoists used to lift the load will add additional weight to the overall lifting requirement.
-
Load swings and dynamic loads: When lifting loads, dynamic forces like momentum and sway may increase the effective load the crane needs to handle, especially when lifting large or bulky items. Cranes need to be capable of handling these dynamic forces without failure.
These factors may add an additional 10–15% to the total weight requirement, depending on your lifting conditions.
c. Calculate the Safety Margin
When calculating the optimal capacity, it’s important to factor in a safety margin. A safety margin is the difference between the maximum load and the crane’s rated capacity, which provides a buffer to account for unexpected loads, improper rigging, or other unforeseen factors.
A general rule of thumb is to add a 20–25% safety margin to the calculated maximum load. For instance, if the heaviest load you expect is 50 tons, you should choose a crane with a capacity of 62.5 tons (50 tons + 25%).
4. Considering the Crane’s Duty Class
Overhead cranes are classified based on their duty cycle, which is a measure of how frequently the crane will be used and how long it will be under load. Duty cycles are categorized from light (A1-A3) to heavy-duty (A7-A8). Each class represents the level of use the crane is designed to handle, and the duty cycle impacts the capacity you choose.
-
Light Duty (A1-A3): Low usage with occasional lifting of relatively light loads.
-
Medium Duty (A4-A5): Moderate usage with regular lifting of medium-weight loads.
-
Heavy Duty (A6-A8): Continuous or near-continuous use with heavy loads.
For heavy-duty operations, you’ll need a crane with a higher capacity and durability. If you plan to use the crane for high-frequency operations or frequent heavy lifts, the heavy duty overhead crane should be designed to accommodate that level of demand.
5. Consider Future Requirements
While determining the immediate needs is essential, you should also consider potential future requirements when choosing your crane’s capacity. For instance, if your business plans to scale up operations, expand its product range, or increase the volume of lifting tasks, it may be wise to opt for a crane with a higher capacity to avoid upgrading in the near future.
A crane with slightly more capacity than required can help avoid bottlenecks in the future and ensure your system can handle increased workloads.
6. Conclusion: The Optimal Capacity
To summarize, determining the optimal lifting capacity for your single girder overhead crane involves understanding your operational needs, calculating the maximum load and considering safety margins, factoring in crane duty cycles, and anticipating future demands.
A crane with the correct lifting capacity will help improve operational efficiency, reduce downtime, and increase overall productivity while ensuring safety. Choosing a crane that is too small can result in overloading, increased wear, and potential safety hazards. Conversely, selecting a crane with excessive capacity may lead to higher costs and less efficient performance.
By carefully evaluating your lifting requirements, considering dynamic forces, and factoring in safety margins and duty cycles, you can select the optimal lifting capacity for your crane, ensuring reliable and safe operation for years to come.
Essential Tips for First-Time Buyers: Avoiding Common Mistakes When Purchasing an Automatic Batching Plant
Investing in an automatic batching plant is a significant decision for many businesses, particularly those in the construction industry. However, first-time buyers often fall prey to various mistakes that can lead to substantial financial losses and unsatisfactory plant performance. This article aims to guide you through the common pitfalls to avoid when purchasing an automatic rmc plant, ensuring that you make an informed and beneficial investment.
Common Mistakes First-Time Buyers Make When Purchasing an Automatic Batching Plant
1. Selecting the Wrong Manufacturer
One of the most prevalent mistakes that new buyers make is opting for the first manufacturer they encounter. With numerous manufacturers available, some may rely solely on attractive marketing strategies, leaving buyers unaware of the actual quality of their products.
To ensure a smart purchase, it’s essential to conduct thorough research on potential manufacturers. Engage with existing customers to gain insights into their experiences with the mobile concrete batching plants. Customer reviews can provide valuable information about the reliability and performance of the plant. If feedback from customers is predominantly negative, or if you find that many users recommend against a particular brand, it’s wise to steer clear of those options. Always prioritize the quality and reputation of the manufacturer over their marketing tactics.
2. Overlooking the Importance of Warranty
Many first-time buyers neglect to check the warranty terms of the automatic batching plant they are considering. They may assume that any plant they purchase will function effectively for years to come. However, an adequate warranty is crucial, even when buying from a reputable manufacturer, like AIMIX Group. Automatic batching plants, like any machinery, may experience breakdowns or defects.
To safeguard your investment, look for a plant that comes with a comprehensive warranty. A long warranty term will not only cover potential repairs but also provide peace of mind. Should any issues arise during the warranty period, the manufacturer should be accountable for repairs or replacements, allowing you to operate your plant without financial concerns.
3. Failing to Conduct Price Comparisons
Another common mistake among inexperienced buyers is the failure to conduct thorough price comparisons. Some buyers may be inclined to purchase the first plant they see, without exploring other options. This can result in overspending, as prices for automatic batching plants can vary significantly among different sellers.
In today’s digital age, comparing prices has never been easier. You can research various manufacturers and their respective prices from the comfort of your home. Browse multiple websites that specialize in selling automatic batching plants and gather quotes. This will enable you to identify affordable options while factoring in shipping costs. By taking the time to compare prices, you can make an informed decision and save significant amounts of money.
4. Ignoring the Significance of Customer Service
For buyers who have not previously operated an automatic batching plant, navigating its complexities can be daunting. Many first-time users may require additional training to understand how to properly utilize the machine. Hiring an expert to provide this training can be expensive, but selecting a seller who offers after-sale services can alleviate this burden.
Always prioritize vendors that provide robust customer service and support following your purchase. A reputable seller should offer training to you or your staff on how to operate the plant. They should also be easily accessible to answer any questions or address concerns you may have after installation. Opting for sellers with strong customer service can make a significant difference in your experience with the equipment.
5. Neglecting to Assess the Plant’s Specifications
Buyers often focus primarily on the price or appearance of the concrete plant for sale without thoroughly assessing its specifications. It’s crucial to ensure that the plant meets your specific production needs and operational requirements. Factors such as production capacity, mixing efficiency, and the types of materials the plant can handle should align with your business goals.
Familiarize yourself with various models and their capabilities. Understanding the technical specifications will help you choose a batching plant that not only fits your immediate needs but also supports your business in the long run.
Conclusion: Making a Wise Investment in Your Batching Plant
Purchasing an automatic batching plant can be a transformative investment for your business, significantly impacting your operational efficiency. By avoiding the common mistakes outlined above—such as choosing the wrong manufacturer, ignoring warranty details, failing to conduct price comparisons, overlooking customer service quality, and neglecting plant specifications—you can make a well-informed decision.
Take the time to research, compare options, and understand all aspects of your investment. With careful consideration, you can choose an automatic mobile batching plant that meets your needs, ensuring a successful operation in the years to come.
Structural Advantages of Trailer Concrete Pumps
Trailer concrete pumps are becoming increasingly popular due to their versatility, cost-effectiveness, and efficiency. These mobile units provide a reliable solution for transporting concrete to construction sites, especially in areas that are difficult to access or require quick, precise placement. In this article, we will explore the structural advantages of trailer concrete pumps, how they improve construction processes, and why they have become a preferred choice for many contractors. Whether you are considering purchasing a concrete pump or exploring the latest models available, understanding these structural advantages can help you make an informed decision.
1. Compact and Mobile Design
One of the most significant advantages of trailer concrete pumps(bomba estacionaria de hormigón) is their compact design, which makes them incredibly mobile and easy to transport. Unlike larger concrete pumps, which can be cumbersome and require heavy machinery for movement, trailer concrete pumps are mounted on trailers, allowing them to be towed behind trucks or other vehicles. This mobility is particularly beneficial in construction projects where access to tight or remote locations is essential. The compact size also makes them ideal for smaller projects, such as residential construction, where space and maneuverability are crucial factors.
1.1 Enhanced Mobility for Different Construction Sites
Because trailer concrete pumps are designed to be towed, they can be easily relocated from one site to another without much hassle. This is especially advantageous for projects that require the equipment to be moved frequently or where the site conditions change over time. The ability to quickly transport the pump to different job sites helps contractors save time and reduces the overall cost of equipment transportation.
1.2 Accessibility in Remote Locations
Trailer concrete pumps are also suitable for working in hard-to-reach areas that might be inaccessible to larger equipment. Whether it’s narrow streets in urban environments or uneven terrain at construction sites, trailer concrete pumps can be easily driven into place, ensuring that concrete can be pumped exactly where it’s needed, even in challenging conditions.
2. Cost-Effective and Versatile
Another reason why trailer concrete pumps have gained popularity is their cost-effectiveness. Compared to larger stationary pumps or boom pumps(autobomba de concreto), trailer concrete pumps are generally more affordable, making them an ideal option for small to medium-sized projects. Additionally, the versatility of these pumps allows them to be used in a variety of construction tasks, further enhancing their value.
2.1 Affordable Investment
For contractors looking to invest in a concrete pump without breaking the budget, a trailer concrete pump is often the most cost-effective option. The initial purchase cost is lower than larger models, and operational costs, such as maintenance and fuel consumption, are also more manageable. This makes trailer concrete pumps an excellent choice for small businesses or those just starting out in the construction industry.
2.2 Multi-Purpose Applications
Trailer concrete pumps can be used in a wide range of construction projects, including residential, commercial, and infrastructure developments. These pumps are suitable for tasks such as pouring foundations, building walls, and even road construction. Their ability to handle different types of concrete and work in various environments makes them a versatile tool for many types of jobs. This flexibility means that contractors can use a single piece of equipment for multiple applications, maximizing its utility and value.
3. Efficient Concrete Placement
Efficiency is key in any construction project, and trailer concrete pumps excel in this area. Their design allows for the fast and precise delivery of concrete, improving productivity and reducing labor costs. These pumps(bombas concreteras) can handle the continuous flow of concrete to the required location, allowing contractors to complete projects more quickly and with greater precision.
3.1 Consistent Concrete Flow
Trailer concrete pumps are designed to maintain a consistent flow of concrete throughout the pouring process. This steady flow ensures that the concrete is evenly distributed, reducing the risk of air pockets and other imperfections. The ability to maintain this consistency is particularly beneficial for projects that require high-quality finishes, such as in the construction of foundations or decorative concrete elements.
3.2 Precision in Hard-to-Reach Areas
When working in challenging locations, such as high-rise buildings or remote construction sites, precision is vital. Trailer concrete pumps are equipped with advanced controls that allow operators to adjust the flow and direction of the concrete, ensuring accurate placement even in difficult-to-access areas. This capability improves the overall quality of the work, reducing waste and the need for rework, which saves both time and money.
4. Durability and Longevity
Durability is another key advantage of trailer concrete pumps. These pumps are built to withstand the harsh conditions often found on construction sites, including exposure to dirt, dust, and extreme weather. The robust design ensures that trailer concrete pumps can perform reliably over time, making them a valuable long-term investment for contractors.
4.1 Heavy-Duty Construction
Trailer concrete pumps are constructed with heavy-duty materials that can endure the stresses of continuous use. This ensures that they remain operational even in challenging conditions, such as high temperatures or muddy environments. The robust design also reduces the likelihood of breakdowns, which can cause delays on construction projects.
4.2 Long-Term Reliability
With proper maintenance, trailer concrete pumps can last for many years, offering reliable performance over time. Their durable design means that contractors can depend on them to deliver consistent results throughout their lifespan. This long-term reliability makes trailer concrete pumps an excellent choice for companies that require dependable equipment for a wide variety of projects.
5. Easy Maintenance and Operation
Trailer concrete pumps are known for their simplicity in terms of both operation and maintenance. These pumps for sale(bomba de hormigón en venta) are designed to be easy to use, with intuitive controls that can be operated by a single person. This reduces the need for highly specialized training and makes it easier for contractors to deploy the equipment on-site without delays.
5.1 User-Friendly Controls
The user-friendly controls on trailer concrete pumps allow operators to quickly learn how to manage the equipment and adjust settings as needed. This ease of use minimizes downtime and ensures that operators can focus on completing their work efficiently. Whether you are working on a small residential project or a larger commercial development, trailer concrete pumps offer straightforward operation that helps keep projects on track.
5.2 Low Maintenance Requirements
Trailer concrete pumps are designed for minimal maintenance, which is a significant advantage for contractors who need reliable equipment without the hassle of frequent repairs. Regular maintenance tasks, such as checking fluid levels and inspecting hoses, are simple and straightforward. This reduces operational costs and ensures that the equipment remains in good condition for longer periods of time.
Conclusion
Trailer concrete pumps offer numerous structural advantages, making them an indispensable tool in modern construction. Their mobility, affordability, versatility, and ability to efficiently place concrete in hard-to-reach areas make them an excellent choice for a wide range of construction projects. Whether you are purchasing a concrete pump for sale or considering adding a trailer concrete pump to your fleet, understanding these structural benefits can help you make the right decision. With their durable design, ease of use, and low maintenance requirements, trailer concrete pumps are sure to continue to be a valuable asset for contractors in the years to come.
Small Self-Loader Mixer vs. Large Stationary Mixers: Productivity Comparison
Small self loader concrete mixers and larger stationary mixers serve distinct roles in construction projects, each with its own set of advantages and limitations. Understanding how these two types of mixers compare in terms of productivity and output is crucial for contractors and construction professionals.
Overview of Small Self Loader Concrete Mixers
Small self loader concrete mixers are compact machines designed for mixing and transporting concrete on construction sites with limited space. They typically feature a self-loading mechanism, allowing operators to load materials directly into the mixer without the need for additional equipment. The mini cement mixer for sale is prized for their maneuverability and versatility, making them ideal for small to medium-sized construction projects.
Overview of Larger Stationary Mixers
Larger stationary mixers, on the other hand, are heavy-duty machines designed for high-volume concrete production. These self loading concrete mixture are typically installed at centralized batching plants or large-scale construction sites. They feature a fixed drum or container where materials are batched, mixed, and discharged. Larger stationary mixers are capable of producing large quantities of concrete consistently and efficiently, making them suitable for large construction projects.
Productivity Comparison
Factors Influencing Productivity
Several factors influence the productivity of concrete mixers, regardless of size. These factors include the mixing capacity, mixing speed, loading and unloading times, and overall efficiency of the machine. Additionally, the skill and experience of the operator play a significant role in maximizing productivity.
Efficiency of Small Self Loader Mixers
While small self loader mixers may have smaller mixing capacities compared to larger stationary mixers, they offer advantages in terms of on-site efficiency and flexibility. These compact self loading mixers can maneuver in tight spaces and deliver concrete directly to the point of placement, reducing the need for additional handling and transportation. Additionally, self-loading features allow operators to batch and mix concrete as needed, minimizing waste and downtime. View more details about mixers here: https://aimixconcretesolution.com/self-loading-concrete-mixer/tanzania/.
Output Comparison
Capacity Differences Between Small and Large Mixers
One of the most significant differences between small self loader mixers and larger stationary mixers is their capacity for concrete production. Larger concrete mixers typically have higher mixing capacities, allowing them to produce larger volumes of concrete in a single batch. In contrast, small self loading cement mixer for sale has limited capacities but excel in producing smaller batches of concrete quickly and efficiently.
Quality and Consistency of Output
While larger stationary mixers may offer higher production capacities, small self loader mixers are known for their ability to produce high-quality concrete consistently. These compact mixers utilize advanced mixing technology and control systems to ensure uniform mixing and proper concrete consistency. Additionally, self-loading features enable operators to adjust mix designs on-site, optimizing the quality of the final product.
How to Install and Maintain Steel Grid Structure
A steel grid structure is a type of architectural framework consisting of a network of intersecting steel beams or bars that are arranged in a grid-like pattern. These structures are commonly used in modern construction projects due to their strength, durability, and ability to cover large spans without the need for internal supports. Steel grid structures are often employed in the construction of roofs, bridges, industrial buildings, and even in specialized applications like sports stadiums or exhibition halls. However, proper installation and maintenance are crucial for ensuring the safety, longevity, and optimal performance of these structures. This article provides a detailed guide on how to install and maintain steel grid structures.
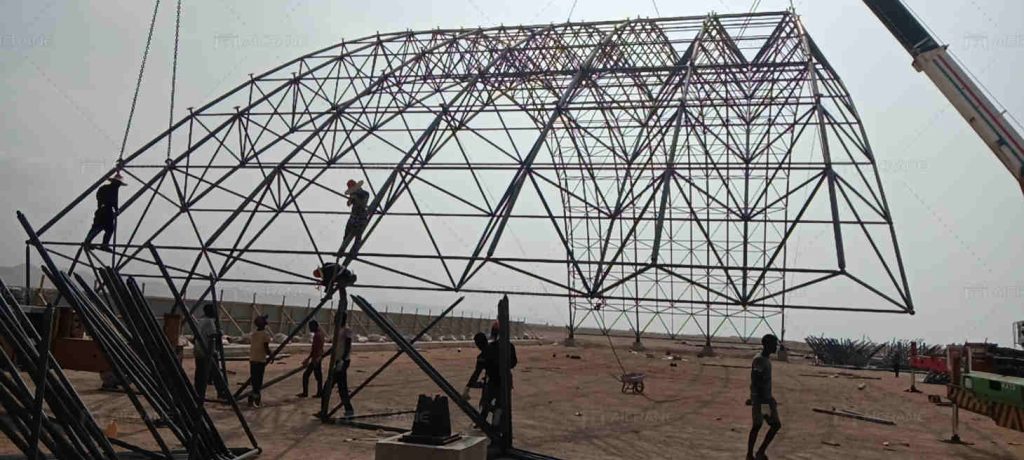
Planning and Preparation for Installation
Before beginning the installation of a steel grid structure, thorough planning and preparation are essential. This ensures that the project proceeds efficiently and meets safety standards.
Design and Engineering
The first step in the installation process is to ensure that the steel grid structure is designed by experienced engineers who can account for factors like load-bearing capacity, material strength, and environmental conditions. The design should consider the grid’s overall geometry, the size and spacing of the beams, and the connections between components. Steel grid structures can vary widely depending on their intended use, so customizing the design to the specific needs of the project is crucial.
Once the design is finalized, an engineering analysis should be performed to calculate the expected loads and stresses on the steel structure. This will ensure that the grid is capable of handling the loads it will be subjected to, such as the weight of the roof, equipment, or other loads.
Site Preparation
The construction site should be cleared and prepared before installation begins. The foundation must be level and capable of supporting the weight of the steel grid structure. Proper groundwork, including excavation and leveling, is essential to ensure that the grid structure will be installed safely and effectively. The steel grid should be positioned to provide adequate support for the roof or floor it will support, with attention to alignment and any potential obstacles.
Material Procurement
The materials for the steel grid structure must be sourced in accordance with the specifications outlined in the design. Steel beams, trusses, and other necessary components must be inspected for quality and integrity before they are delivered to the site. It’s crucial to ensure that the materials meet the required standards to avoid complications during installation.
Installation Process
Once the planning, design, and procurement phases are completed, the actual installation of the steel grid structure can begin. Some manufacturers like Aicrane will provide installation guidance. The following steps outline the typical installation process.
Assembly of Steel Grid Components
The steel grid structure is typically constructed in sections, and these sections must be assembled on-site or pre-fabricated off-site before being transported for installation. Workers should follow the detailed design plans and ensure that all steel components are correctly positioned.
The grid structure is assembled by first placing the primary beams or main supports at their designated locations. These beams will bear the main loads of the grid and serve as the foundation for the entire structure. Next, secondary beams or bars are placed at regular intervals across the primary beams to create the grid pattern.
Connection and Welding
Once the steel grid components are positioned, they need to be connected using bolts, rivets, or welding, depending on the design specifications. Welding is often used to create a stronger and more permanent connection, while bolts or rivets may be used for ease of assembly and flexibility. The welding process should be carried out by certified welders to ensure that all connections are strong and free from defects.
Proper alignment is critical during this stage. Each section of the grid structure must be carefully adjusted to avoid misalignment, which could result in uneven loads and reduced structural integrity. After each connection, the structure should be checked for squareness and stability before moving on to the next phase.
Installation of Support Components
In addition to the steel grid itself, other support components, such as braces, columns, or reinforcement bars, may need to be installed to provide additional stability to the structure. These components are particularly important for ensuring the grid’s resistance to lateral forces, such as wind or seismic activity.
Quality Control and Inspection
Before proceeding with the next phase of construction, it is essential to conduct a thorough quality control inspection to ensure the grid structure has been installed correctly. This inspection should include checks for proper alignment, secure connections, and overall structural integrity. Any defects or issues identified during the inspection should be addressed immediately.
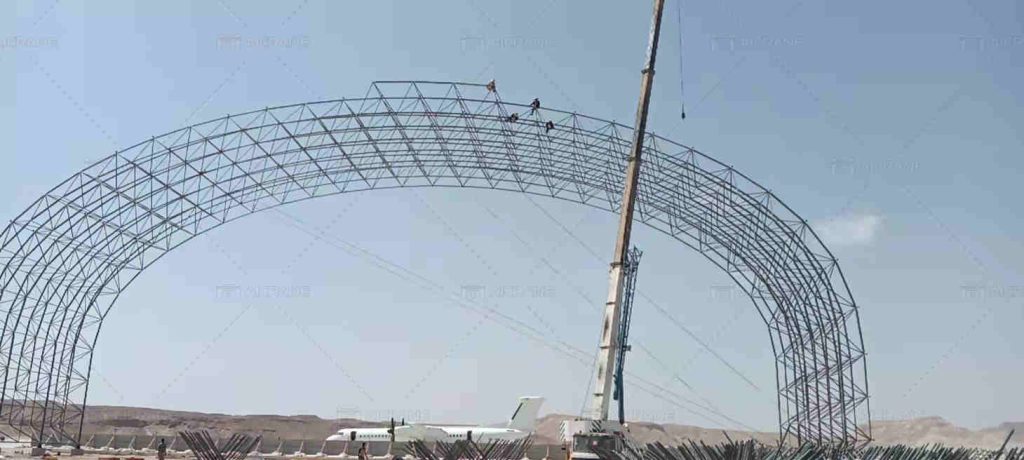
Maintenance of Steel Grid Structures
Once the steel grid structure has been installed, regular maintenance is essential to ensure its longevity, safety, and efficiency. Over time, steel structures can experience wear and tear due to environmental conditions, load-bearing stresses, and other factors. Maintenance can help prevent damage, extend the structure’s lifespan, and ensure it continues to perform at an optimal level.
Regular Inspections
Routine inspections are crucial for identifying any signs of damage or wear that could compromise the integrity of the steel grid structure. These inspections should be carried out by qualified professionals at regular intervals, such as every six months or annually, depending on the structure’s use and exposure to environmental factors.
Inspectors should look for signs of corrosion, especially in areas where water or moisture is likely to accumulate. They should also check for cracks, deformations, or loose connections that could indicate structural issues. If any problems are identified, repairs or replacements should be made promptly to prevent further damage.
Corrosion Protection
Steel grid structures are susceptible to corrosion, especially when exposed to moisture or harsh environmental conditions such as saltwater in coastal areas. To prevent corrosion, steel components should be coated with anti-corrosion materials, such as galvanizing or epoxy coatings. Regular maintenance of these protective coatings is necessary to ensure they remain intact and effective.
If corrosion is detected during an inspection, the affected areas should be cleaned, treated, and re-coated as needed. In severe cases, the corroded sections may need to be replaced entirely.
Cleaning and Lubrication
Dirt, dust, and debris can accumulate on the steel grid structure over time, which can impair its performance and aesthetic appearance. Regular cleaning is essential to maintain the structure’s integrity and appearance. This can be done using pressure washing or other cleaning methods that are appropriate for the material and environment.
Moving parts of the steel grid, such as joints, hinges, or cables, may require periodic lubrication to prevent wear and ensure smooth operation. The correct lubricants should be used to avoid damaging the components.
Load Monitoring
Steel grid structures are designed to bear specific loads, and it’s important to monitor the loads placed on the grid to ensure they do not exceed the design specifications. Overloading the grid structure can lead to deformations, stress fractures, or even catastrophic failure.
Regular load checks should be conducted to ensure that the structure is not subjected to excessive stress. If the load-bearing capacity of the structure is exceeded, adjustments should be made to distribute the load more evenly or additional support should be added.
Repairs and Upgrades
As the structure ages, repairs and upgrades may be necessary. Small issues, such as loose bolts or minor cracks, should be addressed immediately to prevent them from worsening. More significant repairs, such as replacing damaged beams or reinforcing weakened sections, may be required if the grid structure begins to show signs of significant wear.
Upgrades may also be needed as the needs of the building or facility change. For example, the steel structure warehouse may need additional reinforcement if it is being used to support heavier loads, or if new safety regulations require additional structural elements.
The installation and maintenance of steel grid structures require careful planning, skilled labor, and regular upkeep to ensure the safety and longevity of the structure. By following best practices for installation, including proper material selection, precise assembly, and rigorous quality control, you can ensure that your steel grid structure performs optimally. Regular maintenance, including inspections, corrosion protection, and load monitoring, will help extend the lifespan of the structure and prevent costly repairs down the road. With attention to detail and ongoing care, a well-installed and maintained steel grid structure can provide reliable support for many years.
How to Reduce Costs Without Compromising on Bridge Crane Quality
Investing in a bridge crane is a significant decision for businesses that rely on material handling equipment to optimize their operations. While cost considerations are crucial, it is equally important to ensure the crane’s quality meets safety, efficiency, and durability standards. Fortunately, there are ways to strike a balance between cost efficiency and quality. This article explores strategies to help businesses reduce costs without compromising on the quality of their bridge cranes.
1. Understand Your Specific Needs
The first step in reducing bridge crane cost is to clearly understand your operational requirements. Purchasing a bridge crane with unnecessary features or excessive capacity can lead to inflated costs. Here are some questions to consider:
- What is the maximum load you need to lift?
- How often will the crane be used?
- What is the required span and lifting height?
- Will it be used indoors or outdoors?
By identifying these needs, you can avoid over-specifying the crane and ensure you’re paying only for what your operations require.
2. Choose the Right Type of Bridge Crane
Different types of bridge cranes come with varying price points. Single girder cranes are typically less expensive than double girder cranes and are suitable for lighter loads and smaller spans. Conversely, double girder overhead cranes are suitable for heavier loads and longer spans but come at a higher cost.
Evaluate your load capacity and operational needs to select the most cost-effective type of bridge crane. For example, a single girder crane might suffice for a warehouse with moderate lifting requirements, whereas a double girder crane is more appropriate for heavy-duty applications like steel mills or power plants.
3. Opt for Standard Designs When Possible
Customized bridge cranes can be significantly more expensive due to additional design and manufacturing processes. If your requirements can be met with a standard crane design, this can save considerable costs. Standard cranes are also easier to maintain and have readily available spare parts, further reducing long-term expenses.
4. Compare Manufacturers and Suppliers
Not all manufacturers and suppliers offer the same pricing or quality standards. Conduct thorough research to compare different vendors. Factors to consider include:
- Reputation and customer reviews
- Quality certifications and compliance with industry standards
- After-sales support and warranty terms
Request detailed quotes from multiple suppliers and assess the value they offer rather than focusing solely on the upfront cost. A trusted overhead crane manufacturer with competitive pricing can provide high-quality equipment without inflating costs.
5. Leverage Bulk Purchasing or Long-Term Contracts
If your business requires multiple bridge cranes or other related equipment, consider negotiating bulk purchasing agreements or long-term contracts with suppliers. Manufacturers often offer discounts for larger orders, which can help reduce unit costs while maintaining quality.
6. Consider Refurbished or Pre-Owned Cranes
Refurbished or pre-owned bridge cranes can be a cost-effective alternative to purchasing brand-new equipment. Many reputable suppliers offer refurbished cranes that meet safety and performance standards. Ensure the crane is thoroughly inspected and certified before purchase to avoid compromising on quality.
7. Focus on Energy Efficiency
While the initial cost of an energy-efficient bridge crane might be slightly higher, the long-term savings on operational costs can be substantial. Look for cranes equipped with features such as variable frequency drives (VFDs) or energy recovery systems. These technologies reduce energy consumption and lower operational expenses, offsetting the initial investment.
8. Optimize Installation Costs
Installation costs can add significantly to the total expenditure. To reduce these costs:
- Work with suppliers that offer on-site or remote installation guidance.
- Ensure your site is prepared and equipped for installation to minimize delays.
- Collaborate with experienced local installation teams to avoid unnecessary expenses.
Proper planning and coordination can help streamline the installation process and reduce associated costs.
9. Invest in Preventative Maintenance
Quality bridge cranes require regular maintenance to perform optimally. Skimping on maintenance can lead to expensive repairs or replacements down the line. Implement a preventative maintenance program that includes regular inspections, lubrication, and timely replacement of worn-out parts.
A well-maintained crane not only ensures operational efficiency but also extends its lifespan, reducing the need for costly replacements.
10. Train Your Operators
Operator errors can lead to unnecessary wear and tear or even accidents, resulting in additional costs. Investing in comprehensive operator training can:
- Improve the efficiency of crane operations
- Minimize the risk of damage to the crane and loads
- Enhance workplace safety
Well-trained operators can help your business get the most out of your bridge crane, ensuring it operates reliably for years to come.
11. Take Advantage of Tax Incentives and Financing Options
Many governments offer tax incentives or subsidies for businesses investing in capital equipment, including electric overhead cranes. Research available programs in your region and consult with a financial advisor to take advantage of these opportunities.
Additionally, consider financing options offered by manufacturers or financial institutions. Spreading the cost over time can make high-quality equipment more affordable without straining your budget.
12. Negotiate for Extended Warranties
Extended warranties provide peace of mind and can reduce long-term maintenance and repair costs. Negotiate with your supplier to include an extended warranty in the purchase price. A comprehensive warranty ensures that any defects or issues are addressed promptly without additional expenses.
13. Plan for Future Scalability
While cost reduction is important, it’s essential to consider future growth and scalability. Investing in a crane that can be upgraded or modified as your business expands can save money in the long run. For example, choose a design that allows for easy integration of advanced technologies or increased capacity if needed.
Conclusion
Reducing costs without compromising on bridge crane quality requires a combination of strategic planning, careful selection of suppliers, and an emphasis on long-term value. By understanding your specific needs, choosing the right type of crane, and focusing on energy efficiency and maintenance, you can optimize your investment while ensuring reliable and safe operations. Balancing cost and quality not only saves money but also positions your business for sustainable growth and efficiency.
Optimizing Your Workshop with Double Girder Overhead Crane
Double girder overhead cranes are a versatile and powerful solution for optimizing workshops and industrial environments. These cranes provide enhanced lifting capabilities, greater stability, and efficient space utilization, making them ideal for a range of applications, from heavy-duty manufacturing to precise material handling tasks. If you’re looking to enhance your workshop operations, understanding how to optimize your processes with a double girder overhead crane is key. Here’s how you can maximize the efficiency, safety, and productivity of your workshop by implementing a double girder overhead crane.
Understanding the Benefits of Double Girder Cranes
A double girder overhead crane consists of two parallel girders supported by end trucks that run on overhead rails. This design provides several advantages over single girder cranes, including:
- Higher Lifting Capacities: Double girder cranes can handle much heavier loads, often up to 100 tons or more. The extra support provided by the second girder allows for greater lifting power and the ability to move heavy materials without compromising safety or performance.
- Greater Span and Hook Coverage: These cranes can cover larger areas due to the increased span between the girders. This allows them to serve a wider workspace without the need for additional equipment or overhead structures.
- Better Stability and Safety: The added girder provides increased structural integrity, reducing the chances of sway or instability during lifts, particularly with heavy or uneven loads. This leads to safer operations, especially in challenging environments.
- Flexibility: Double girder cranes are versatile and can be used for a variety of tasks, from lifting heavy loads to precise material handling. They can also be designed for specialized applications, such as working in high-clearance spaces or in harsh environments.
Maximizing Space Utilization
One of the primary advantages of a double girder overhead crane is its ability to optimize space. With the crane’s track mounted on the ceiling, the workshop floor remains clear of obstructions. This makes it easier to move materials across the workspace without interference from other equipment.
- Efficient Layout: By utilizing the full height of your workshop, a double girder heavy duty crane allows you to use the space below for storage, assembly lines, or other equipment. This is particularly useful in workshops where floor space is limited or needs to be optimized for other processes.
- Multi-Point Lifting: Double girder cranes can handle multiple lifting points simultaneously, which increases productivity by enabling several tasks to be performed in parallel. For instance, while one load is being moved, another can be lifted or lowered in a different part of the workshop, reducing downtime and increasing throughput.
Improving Productivity with Precision and Control
Double girder overhead cranes are equipped with advanced control systems that allow for greater precision and control in lifting and lowering operations. This level of control is particularly important for tasks that require delicate handling or precise placement of materials, such as in assembly lines or research and development workshops.
- Smooth Lifting and Lowering: The design of double girder cranes ensures that the load is lifted and lowered smoothly, reducing jerky movements that could damage materials or components. This is especially critical for handling sensitive or fragile items, where precision is key.
- Variable Speed Control: Many double girder cranes are equipped with variable speed drives, which allow operators to adjust the lifting speed depending on the specific task. This gives operators the flexibility to work efficiently while maintaining control over load movement.
This precision and control not only improve the quality of work but also reduce the risk of errors and accidents, ultimately leading to a more productive workshop.
Enhancing Safety Features
The safety of your team is a critical concern in any workshop. Double girder cranes are equipped with advanced safety features that help prevent accidents and ensure smooth operations:
- Overload Protection: Many double girder cranes come with overload protection systems that prevent the crane from lifting loads beyond its capacity. This reduces the risk of mechanical failure or accidents caused by overloading.
- Anti-Sway Mechanisms: Cranes with anti-sway systems reduce the swinging motion of loads, particularly when moving heavy or bulky items. This helps maintain the stability of the crane and ensures that operators and nearby workers remain safe.
- Emergency Stop and Warning Systems: Double girder cranes are often equipped with emergency stop functions and warning systems such as lights or alarms to alert workers when the crane is in operation or approaching a critical point.
By implementing these safety features, you not only protect your team but also prevent costly damage to materials and equipment.
Customizing Your Crane for Specific Tasks
Double girder cranes are highly customizable, which allows you to tailor them to meet the specific needs of your workshop. Depending on the types of materials you handle and the tasks you perform, you can adjust several components:
- Lifting Equipment: Choose from various lifting devices such as hooks, grabs, magnets, or custom attachments to suit your needs. This flexibility ensures that your overhead crane machine is equipped for the type of material you are handling, from steel beams to containers.
- Control Systems: You can customize the crane’s control system to match your operational requirements. Whether you need manual, semi-automatic, or fully automated operation, customizing the control system increases efficiency and ease of use.
- Size and Capacity: Double girder cranes come in a range of sizes and load capacities, so you can select one that aligns with your workshop’s needs. For example, a larger crane with a higher load capacity might be required for lifting heavy steel, while a small overhead crane could be more efficient for lighter materials.
This level of customization ensures that your overhead crane is optimized for your specific application, improving overall operational efficiency.
Reducing Maintenance Costs
Proper maintenance is crucial to the long-term efficiency of any crane. Double girder cranes are designed to be durable, with robust components that require less frequent repairs. To further reduce maintenance costs:
- Scheduled Inspections: Implement regular inspection and maintenance schedules to check for wear and tear, ensuring that components such as motors, wires, and lifting mechanisms are functioning properly.
- Lubrication and Cleaning: Regular lubrication of moving parts reduces friction and prevents premature wear, while keeping the crane clean helps to extend its lifespan and prevent the accumulation of dirt and debris that could impair its operation.
By staying on top of routine maintenance, you can keep your double girder crane running smoothly, reducing downtime and avoiding costly repairs.
Conclusion
Optimizing your workshop with a double girder overhead crane can significantly enhance productivity, safety, and space utilization. With its superior lifting capacity, customizable features, and ability to handle heavy loads with precision, a double girder crane offers a wide range of benefits for industrial and manufacturing environments. Investing in a double girder crane not only improves operational efficiency but also enhances the safety and reliability of your workshop, allowing your team to work smarter and safer.
Affordable Steel Warehouse Structures for Sale: Maximizing Your Budget
In today’s fast-paced business environment, having an efficient and reliable storage solution is essential for companies across various industries. Steel warehouse structures offer durability, flexibility, and cost-effectiveness, making them an attractive option for businesses looking to maximize their budgets. This article explores the benefits of affordable steel warehouse structure for sale, how to find the best deals, and tips for making the most of your investment.
Why Choose Steel Warehouse Structures?
Steel warehouse structures have gained popularity due to their numerous advantages over traditional building materials. Here are some key benefits:
- Durability: Steel is inherently strong and resistant to environmental factors such as mold, pests, and extreme weather conditions. This longevity ensures that your investment remains sound over time, reducing maintenance and replacement costs.
- Cost-Effectiveness: Steel structures typically have lower construction and maintenance costs compared to wood or concrete buildings. Their prefabricated components can be assembled quickly, minimizing labor costs and reducing the overall time to completion.
- Flexibility: Steel warehouses can be designed to accommodate various layouts and sizes, making them adaptable to different business needs. Whether you require open floor space for storage or specific sections for office space, steel structures can be customized to fit your requirements.
- Energy Efficiency: Modern steel warehouse designs often incorporate insulation and energy-efficient systems, leading to lower energy bills and a smaller environmental footprint. This not only helps the planet but also contributes to long-term savings.
Finding Affordable Steel Warehouse Structures for Sale
To maximize your budget while purchasing a steel warehouse structure, consider the following strategies:
- Research Suppliers: Start by researching reputable suppliers that specialize in steel warehouse structures. Look for companies with positive reviews, a solid track record, and transparent pricing. Request quotes from multiple suppliers to compare costs and options.
- Explore Used or Refurbished Structures: Purchasing used or refurbished steel warehouses can significantly reduce your investment costs. These structures are often available at a fraction of the price of new ones and can still provide the durability and functionality you need. Ensure that any used structures come with proper documentation regarding their condition and history.
- Consider Modular or Prefabricated Options: Modular or prefabricated steel warehouses are designed for quick assembly, reducing construction time and labor costs. These structures often come with pre-engineered designs that meet building codes, making them a cost-effective solution for businesses on a budget.
- Look for Promotions and Discounts: Many suppliers offer seasonal promotions, discounts for bulk purchases, or financing options. Keep an eye out for these opportunities, as they can significantly lower your overall costs.
Maximizing Your Budget: Tips for Cost-Effective Solutions
Once you’ve found affordable steel warehouse structures for sale, consider the following tips to maximize your budget further:
- Plan for Future Growth: When selecting a steel warehouse structure, consider your long-term needs. Choosing a larger or expandable design can save you money in the future, as you won’t need to invest in additional structures as your business grows.
- Invest in Quality: While it may be tempting to opt for the lowest-priced option, investing in high-quality materials and workmanship will pay off in the long run. Quality structures will require less maintenance and offer better performance over time.
- Evaluate Financing Options: Many suppliers offer financing plans to help spread the cost of your investment over time. Explore these options to find a payment plan that aligns with your budget and cash flow.
- Factor in Additional Costs: When budgeting for your steel warehouse structure, don’t forget to account for additional costs such as site preparation, permits, and utility connections. Having a comprehensive budget will help you avoid unexpected expenses. Aicrane has been in steel structure business for many years, offering reliable steel structure solutions to suit different requirements, and you can contact the company to get more details and steel structure price.
Consider Location and Accessibility
The location of your steel warehouse can significantly impact overall costs, including transportation, site preparation, and accessibility. Choosing a site with easy access to major transportation routes can minimize logistics costs and improve efficiency.
Additionally, ensure that the site is properly zoned for your intended use, as zoning regulations can affect construction timelines and costs. Collaborating with local authorities can help streamline the permitting process and avoid potential delays.
Conclusion
Investing in an affordable steel warehouse structure is a smart move for businesses looking to maximize their budgets while ensuring reliable storage solutions. With their durability, flexibility, and cost-effectiveness, steel warehouses are a practical choice for various industries.
By conducting thorough research, exploring used options, and maximizing your budget with strategic planning, you can find the ideal steel warehouse structure that meets your needs without breaking the bank. In a competitive market, a well-chosen steel warehouse can enhance your operational efficiency, enabling your business to thrive for years to come.